Always on the cutting edge of materials and designs, Richard Mille this year surprises us again — this time in tune with the ultra thin trend — as he pushes horological boundaries by releasing the ultra-thin, skelotonized RM 67-01 Automatic Extra Flat watch.
To power the ultra-thin piece, Richard Mille has developed an entirely new in-house movement with its engineers in Les Breuleux. Titled the CRMA6, the new movement is only 3.6 mm thick. Additionally, and in keeping with Mille’s history of working with exotic and durable metals, the base plate and bridges have been constructed from grade 5 titanium and finished with a combination of grey and black electro plasma treatment. The numerals also present an interesting story. They are crafted from solid metal, filled with Luminova and mounted on two linked and rigid titanium rails attached directly to the movement.
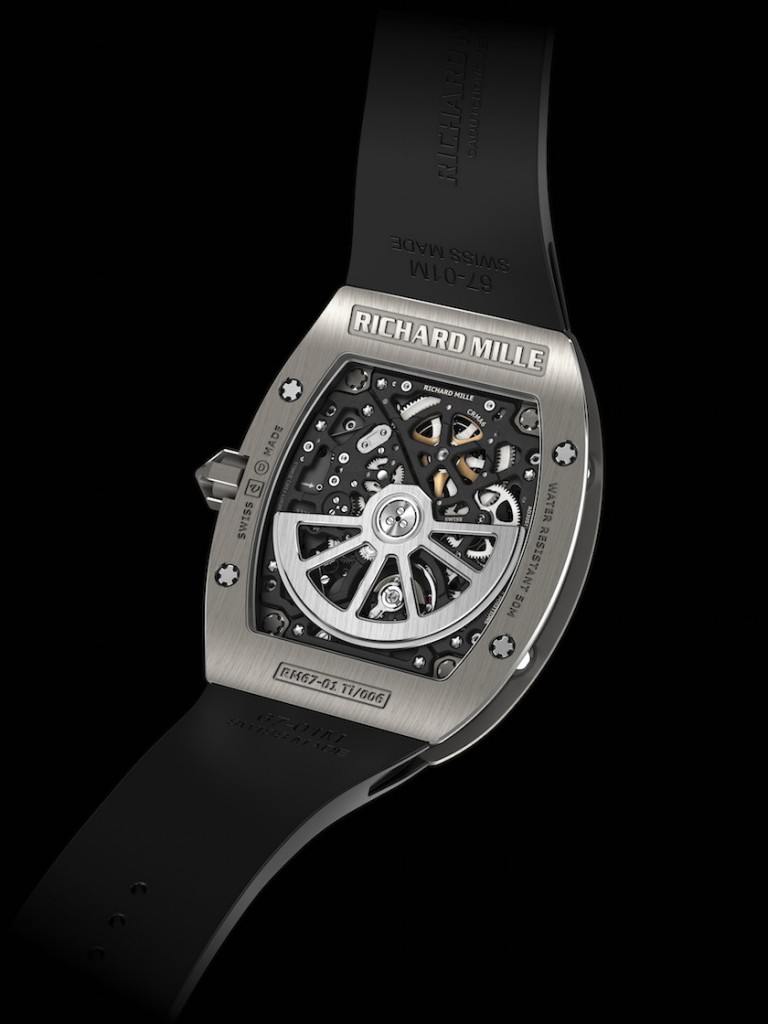
CALIBRE CRMA6: automatic skeletonized winding movement with hours, minutes, date and function indicator. It features a platinum rotor
A unique innovation in the design of the movement has been the incorporation of involute profiles for the going train. What does that mean? Simply put it means that the profiles of the teeth of the gears are involutes of a circle or stated otherwise, slightly curved. The curvature allows for constant contact between gears to allow for efficient transfer of energy. The incorporation of involute profiles is typically found in the auto industry and highly efficient cars, but less so in watch making, making this piece all the more unique.
Not surprisingly, the miniaturization of the classic tonneau shaped case requires additional production time. To chronicle the additional time, an additional 6 hours of machining time, weeks of preliminary preparation for the 68 different stamping operations required for the bezel, case band and back bezel are required. The machine tooling process requires 8 days of adjusting the machines for the bezel, 5 days for the case band and 5 days for the back bezel. Prior to this process, developing a methodology for carrying out this series of operations took 145 hours, the drawings for the tools 130 hours, and implementation 180 hours. Each case represents more than 215 separate machining operations. After the process has been completed, the watch case will be brushed and polished by hand. The sapphire crystal will be attached and undergo water resistance testing before being disassembled for the final quality control test. Only then will the movement be mounted to the case which represents another 8 hours of work.
The watch offers 50 hours of power reserve and features a function indicator that allows the wearer to see the winding, date setting and hand setting positions as the crown is pulled out. Each position is indicated via a hand at 2:00 displaying the functions: W (Winding) – D (Date) – H (Hand setting). Thew watch is further equipped with a free spring balance with variable inertia that helps resist shocked offers better chronmetric results. The rotor is crafted platinum. With the winding system OneWay® with ball bearings in ceramic, the barrel can be efficiently wound while maintaining compact dimensions of the extra flat skeletonized movement.