
Junghans 1972 Competition Quartz Edition Lemon.
Every watch brand has a somewhat different process for creating watch dials. And, in fact, some brands don’t create their own dials at all. They purchase them from companies that are experts at dial making. Some of the top Swiss dial makers have been in business for way over half a century and have a lot to offer brands – creating customized colors, sizes and shapes to fulfill orders.
While we eagerly anticipate the soon-to-be released watches coming up at Watches & Wonders Geneva, we thought it would be fun to take a closer look at how watch dials are made.
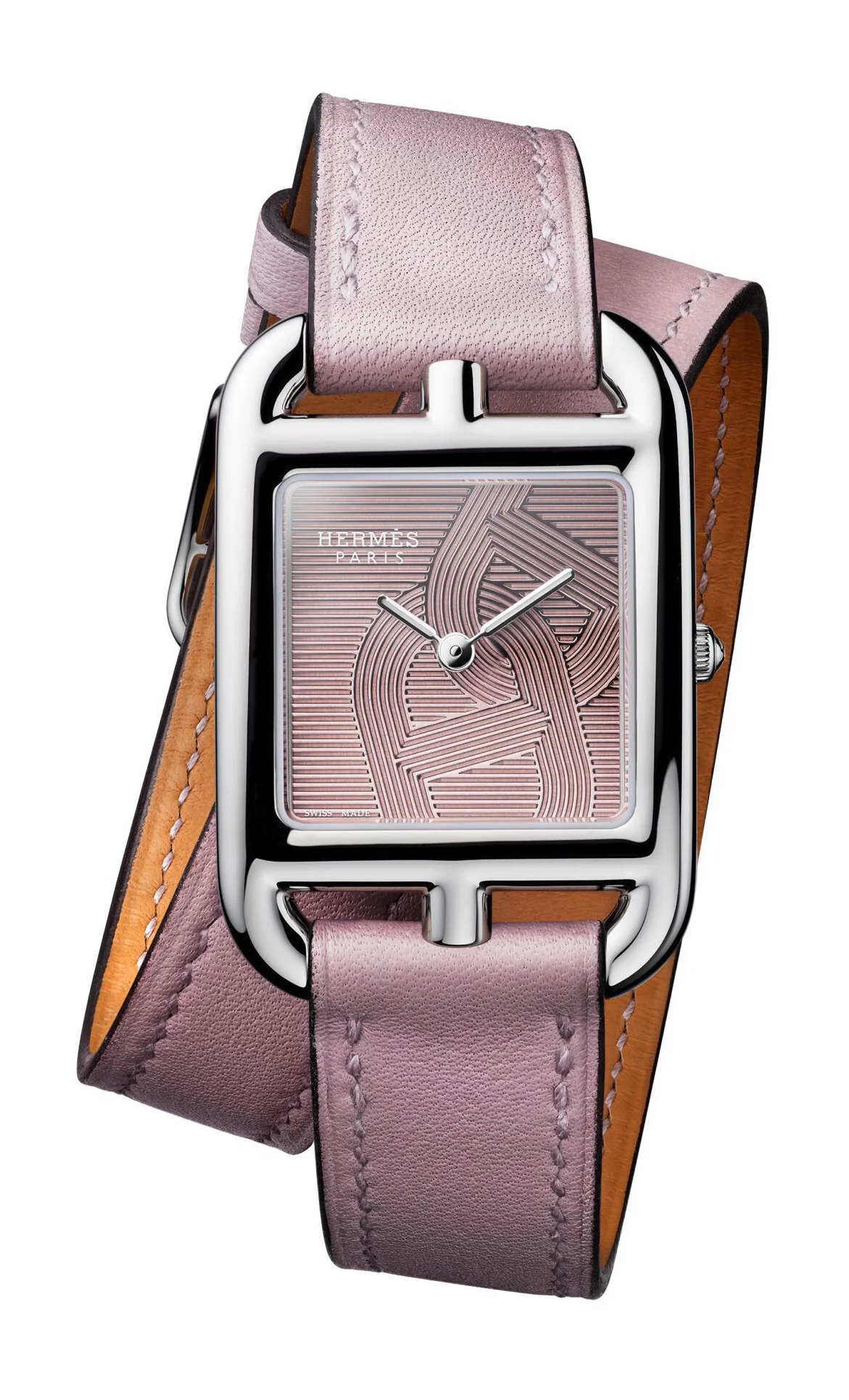
Hermes Cape Cod
Brands like Hermes, for instance, owns one of the best dial makers in Switzerland: Natéber, located in the heart of the watchmaking region of La Chaux-de-Fonds. This company has been crafting dials for just about 50 years and are experts at it.
In their workshops, every Hermes dial experiences just about 60 different steps from start to finish depending on the dial. The dial maker understands the intricacies of the base materials used for dials, including brass, gold, mother of pearl and precious stones. He or she knows how the material will react to being cut, drilled, engraved, painted or polished.
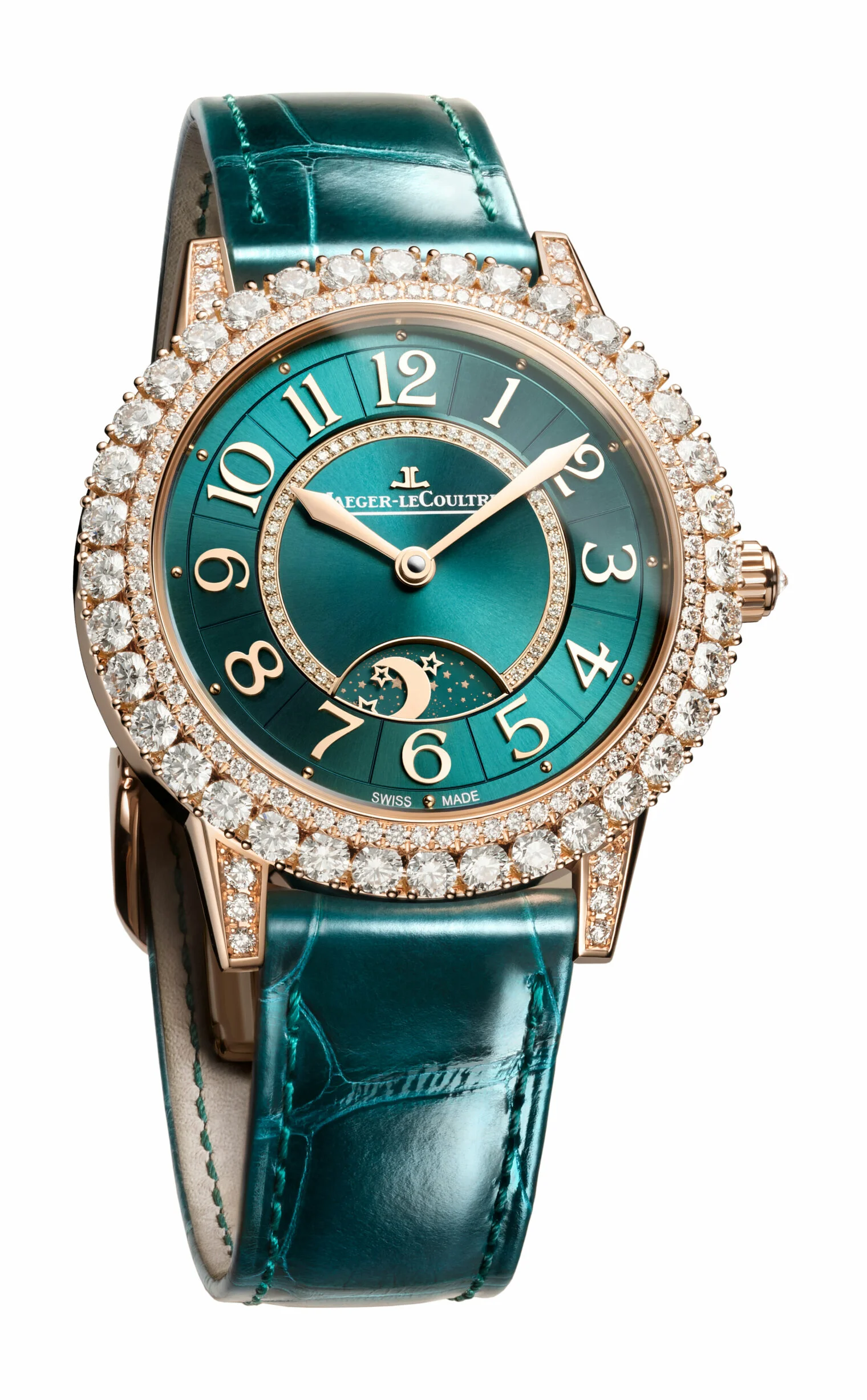
Jaeger-LeCoultre Rendez-Vous Dazzling Night and Day watch
So, the start of each dial begins with selecting the base material. From there, dozens of pairs of hands will work on the final creation. Once the dial material is selected, the dial is cut, sometimes, if holes are needed for feet for the numerals or for window aperture displays, they are cut at this point in time. This is the case with watches with raised numbers or markers. The markers are hand applied and fixed to the dial with tiny feet that slip into a pre-drilled space.
After cutting, the dials then journey through a series of at least seven other departments that range from polishing to engraving or engine turning to achieve a sunray or other pattern, galvanic plating or varnishing to achieve the color, and, if applicable, gem setting for dials with diamond markers or accents and more.
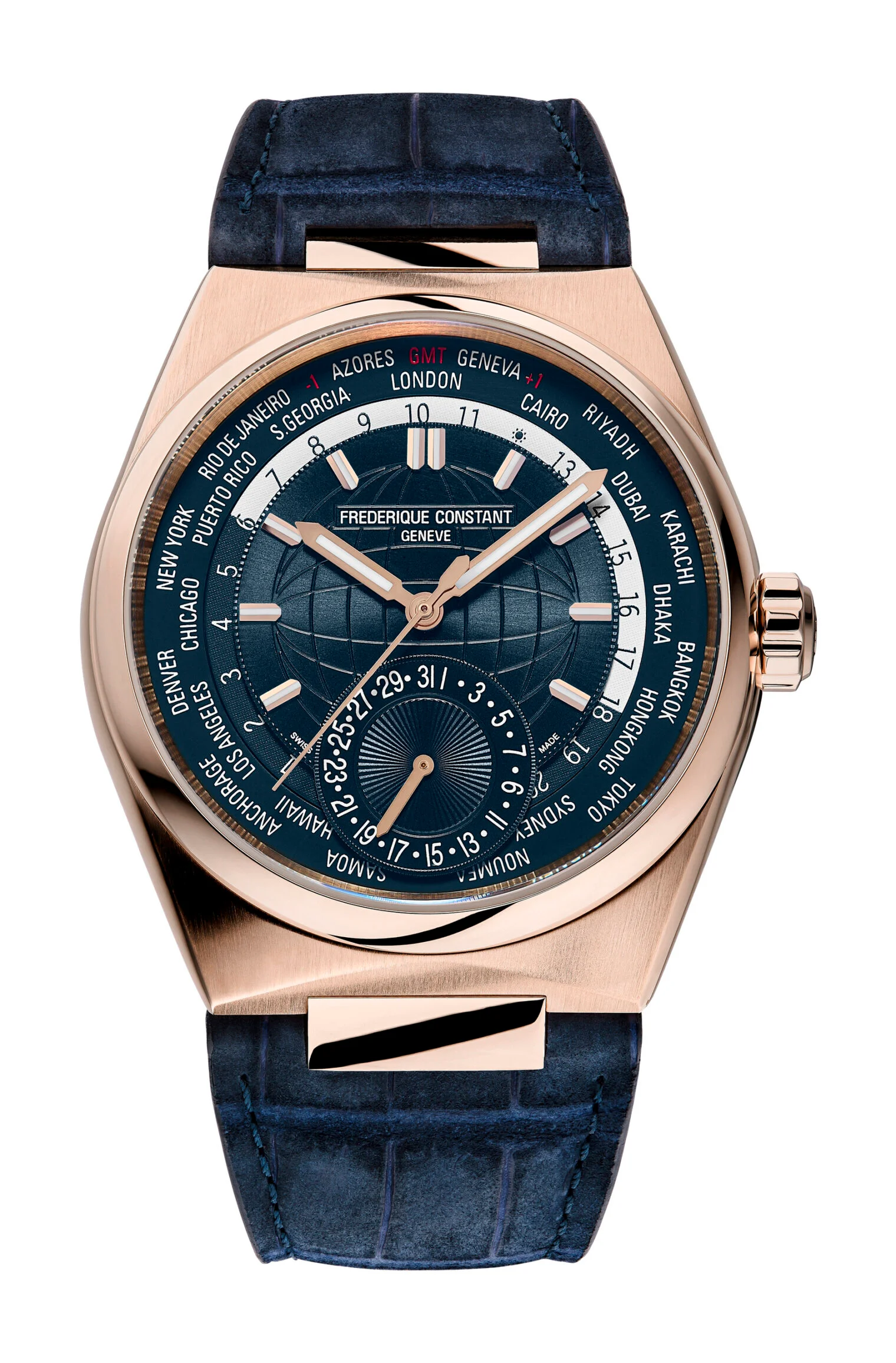
Frederique Constant Highlife World Timer watch
For Metiers d’Arts dials, those are typically hand painted or hand lacquered or enameled and follow a different course than galvanic plating. Often the hand-painting is done by an outside artisan specializing in the different techniques, but some brands have their own Metiers d’Arts workshops where they complete all the dial steps in house.
Once the painting or colorizing of a dial is done, the numbers are put into place. As mentioned, for watches whose markers or numerals are raised, the numerals are hand-set into place using feet that are inserted into the pre-cut holes. For watches with markers that are not raised, the hours are generally transferred onto the dial using a very precise inking process. The perfect amount of pressure has to be applied to ensure every dial is consistent. Lastly, the hands are put in to place by hand using tiny tweezers.
Any potential dust is blown away and the dial is set into place on the watch – soon to air-blown again and then covered and protected by the crystal.

IWC Pilot’s Watch