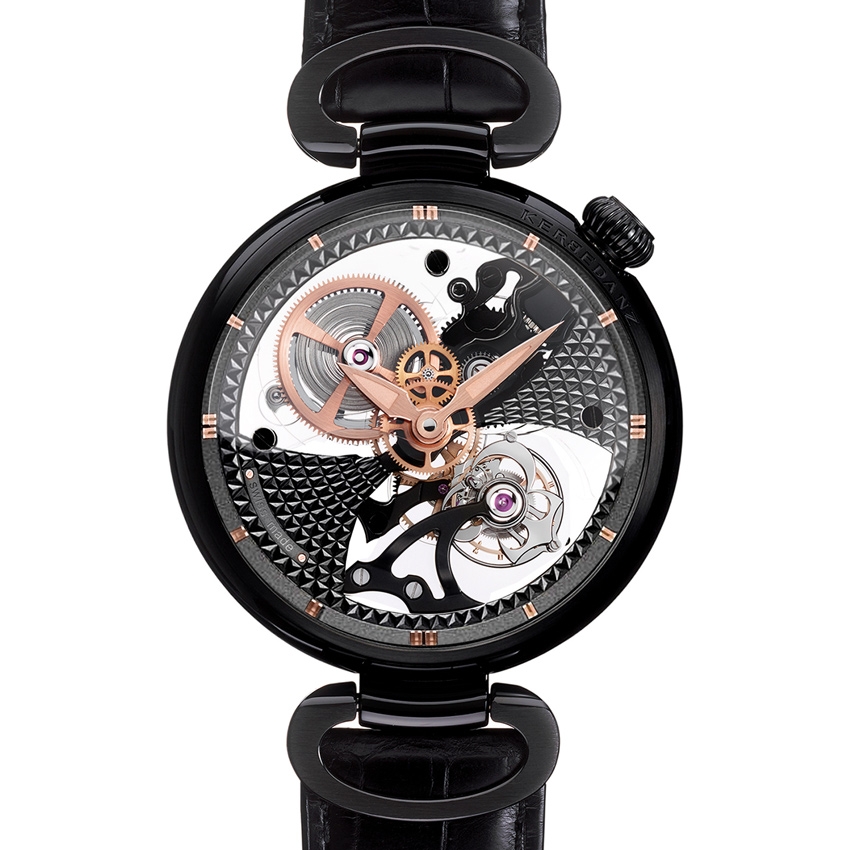
Kerbedanze Skeleton watch. Black watches get their color from a variety of processes, including DLC, PVD and ceramic or alloys made in black.
Happy Halloween. Typically this is a day we take a look at skull watches, skeleton watches, or serpent watches. However, we opted for a different tact this year — a close up look at how black watches get their black color. As an educational piece, this topic is timeless and is one we answer questions about regularly. Essentially, a black-clad watch is one that is either a base metal coated in one of several ways to achieve the black finish, or is a black material such as ceramic, carbon fiber, or other high-tech alloy. Here we take a look at these various stealth options watch brands use to clad their timepieces in the mysterious black of night.
Depending on the watch and the brand, the black color is obtained in one of a variety of manners. As mentioned above, certain luxury brands turn to black materials that are black by nature or that are created in black for a fully black case. These include carbon fiber, black ceramic, layered carbon, or some other space age or automotive racing inspired alloy. With the exception of ceramic, these are usually expensive to create and so are mostly reserved for the luxury end of the spectrum. Hardened engineered ceramic is more affordable, but don’t be fooled, some brands take their ceramic to even higher heights — requiring much more research and development, and time — resulting in higher retail prices.
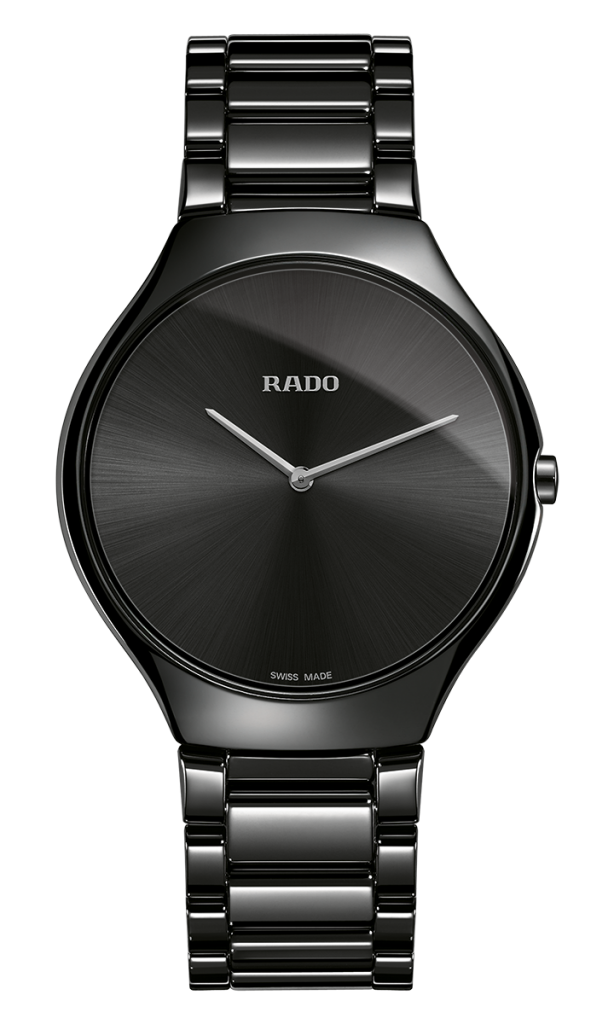
Rado was one of the first brands to work with high-tech ceramic for its watches, such as this recently released Rado True Thinline watch.
Understanding PVD Coating
Generally, however, most watch brands achieve their black cases by using a base metal such as titanium or steel for the case and then treating it with a PVD or DLC process. PVD coating, or Physical Vapor Deposition coating, defines a variety of vacuum coating methods wherein a black coating or thin film of black is applied to the case and bracelet (if applicable). This coating generally also adds a protective barrier.
Essentially, PVD coating vaporizes specialized materials through a high-tech vacuum process and deposits a thin layer on the case. It is accomplished by introducing reactive gasses (nitrogen, oxygen or hydrocarbon-based) to the metallic vapor, to create the coating thanks to a chemical reaction. For this reason, PVD coating is done in a specialized reaction chamber. There are several different methods of PVD coating that include Arc or thermal evaporation, ion beam deposit or ion plating, or sputtering.
By adding a PVD coating, the material is generally strengthened, hardened and garners increased resistance to water, wear and tear, and friction. PVD generally cannot be removed once it is applied and it won’t wear off. It also gives the watch a great stealth look thanks to its polished appearance. PVD can also be created with a matte surface if desired.
Understanding DLC Carbon
DLC is an acronym for Diamond Like Carbon, which is a process most often used on more expensive timepieces made of precious metals, as it is a more expensive process. In Diamond Like Carbon, amorphous carbon materials with properties similar to diamonds (hardness, scratch-resistance, etc.) is applied as a coating to the watch case. There are several different forms of DLC, but all involve using hybridized carbon atoms to varying degrees. The different polytypes of carbon atoms are mixed and result in a substances that is amorphous, flexible and bonds to the metal. These cases are then extra hard and strong and can weather abrasive treatment. Here again, the treatment is applied within a vacuum environment.
All of these processes are employed by watch brands today to create mysteriously alluring black watches.