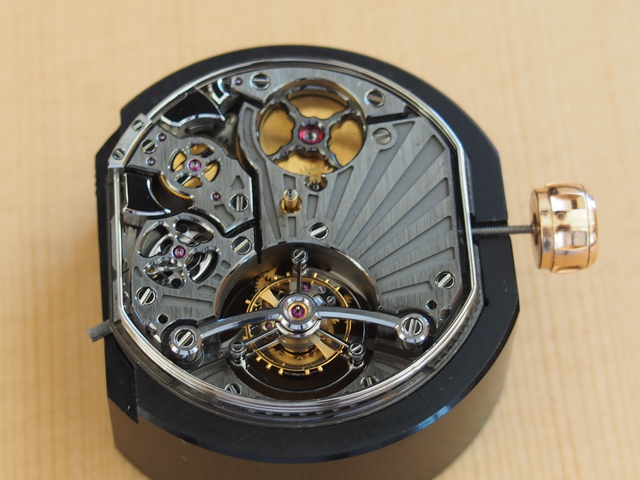
The high-watchmaking division of Bulgari is where four masters create the tourbillons and chiming pieces. (Photo: R.Naas,ATimelyPerspective)
Earlier this year, we had the unique opportunity to go where few have ever gone before: inside the Bulgari Manufacture. I wrote about that experience in IW Magazine, and now, we bring some of that insight to our faithful readers at ATimelyPerspective.
This Italian-born Bulgari (founded in Rome in 1884) has been bringing exceptional watches to the forefront in recent years, with some world-record setting timepieces joining the high-jeweled and haute horology ranks. Much of that growth and development is the result of strong leadership — after all the brand is under the vigilant eye of veteran watch industry executive Jean-Christophe Babin, whose keen knowledge of the industry, eye for product and lust for cutting-edge technology has brought the brand to all new levels. Under his leadership, this brand has—in the past two years alone – unveiled both a world record-setting haute-horology watch with the Octo Finissimo Tourbillon, and at this year’s BaselWorld, with the Octo Finissimo Minute Repeater, which lays claim to the title of the worlds’ thinnest hand-wound Minute Repeater. The Caliber 362 consists of 362 parts and is just 3/12mm thin. When cased, the entire titanium watch — of which just 50 will be made — measures just 6.85mm in thickness.

The haute horology division, where world-record watches are made, sits on the top floor of the Bulgari Manufacture with sweeping views of the landscape. (Photo: R. Naas, ATimelyPerspective)
”It is essential for a top watchmaking brand to be easily identifiable as a brand from a glance, and to do that you must have key pillars, lines whose architecture speaks volumes,” says Bulgari CEO Babin. “Our four pillars include the Octo and the Serpenti – both of which we are building upon this year…. The beauty of Bulgari is to bring a bit of surprise to our consistent identity,” says Babin, adding that the ability to craft such a masterpiece lies, in part, in the brand’s purchase 16 years ago of the Daniel Roth/Gerald Genta workshops.
Since that acquisition in 2000, Bulgari has taken the technical knowledge inherent in those brands and integrated it into its technical plan – keeping only the best designs and inventions. What has really propelled the brand to its newly enjoyed status as a true luxury watchmaker, though, is its incredible commitment to becoming fully integrated, to investing in substantial R&D and to its ability to hire some of the best master artisans available.
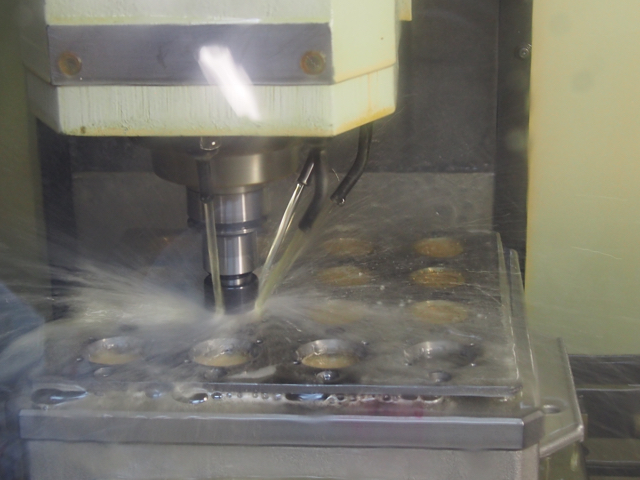
Like other watch brands, Bulgari deftly blends state-of-the-art machinery and CNC machines with hand craftsmanship. (Photo: R.Naas, AtimelyPerspective)
“With a strong base, we were able to build and develop new things thanks to the expertise of our watchmakers and design team,” says Babin. “The past decade has been one of great growth and savoir faire. We have invested fully in R&D and have built our workshops to be fully integrated.”
Indeed, a visit to the Bulgari workshops (a hallowed place that few get to visit) is a real eye-opener and a testament to a deft blend of integrated technology and hand craftsmanship. The Bulgari watch brand workshops – like many Swiss brands – are spread out in the Jura Mountains where the 350-people strong workforce makes everything from movement parts to dials, cases and bracelets internally.
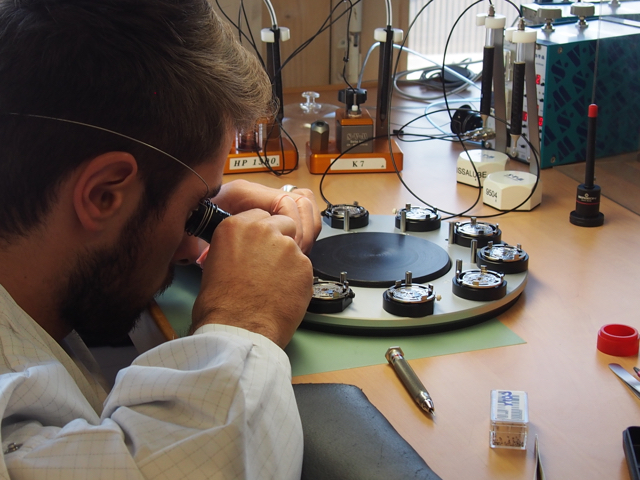
Computerization helps the watchmakers at Bulgari remain incredibly efficient in channeling the work process of assembling movements. (Photo: R. Naas, ATimelyPerspective)
There is a main factory in Le Sentier where the movements (especially the Caliber 191, the ultra-thin Finissimo, and the complicated watches) are made; the assembly workshops and headquarters buildings are in Neuchatel; case and bracelet Manufacture is in Saignelégier; ;the dial-making workshops are in LaChaux de Fonds.
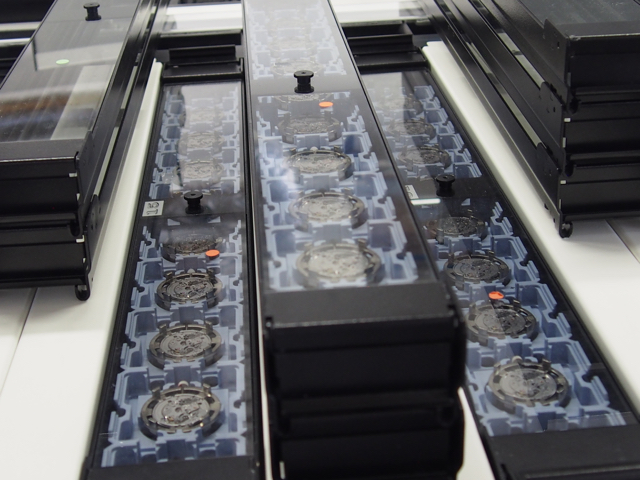
In the main portion of the Bulgari workshops, the mainstay movements are tracked and passed along computerized rails –much like a tiny city of calibers. (Photo: R. Naas,ATimelyPerspective)
It is in the workshops in Le Sentier that most of the important action takes place. Here, the Octo Solotempo movement, Caliber 191, was born. Created about three years ago, it was Bulgari’s first fully in-house-made mechanical movement with automatic winding and instantaneous date. The meticulously finished movement has become the workhorse of the brand, powering many a timepiece.
In a special section of the workshops, more than 40 watchmakers produce this movement for the brands tens of thousands of watches built annually. It is a well-oiled machine, with each and every movement — bar coded from the beginning — undergoing dozens of watchmaking steps, multiple machine- and watchmaker-checked quality controls and more.
Even more impressive is the blend of state-of-the-art machinery and old-world craftsmanship. Movement parts and calibers are finely finished using a variety of techniques by hand and by machine. All of the angling is done by hand, though, and even the tools the specialists use are made by him or her to ensure the best fit.
It is in the finishing that one can easily see why a mechanical, hand-finished watch costs what it does. The fine angling and finishing demands deep concentration, and hundreds of hours of unique skills go in to finishing one piece. At the haute horology level, it takes 20 hours just to finish the three pieces and the tourbillon carriage bridges for a single tourbillon watch—so that only two complete sets can be made in a week.
In addition to the superb finishing departments in the Le Sentier workshops, this building is also where the complicated watchmaking takes place – with the tourbillons, perpetual calendars and other specialty pieces being created by a team of 10 high-horology watchmakers.
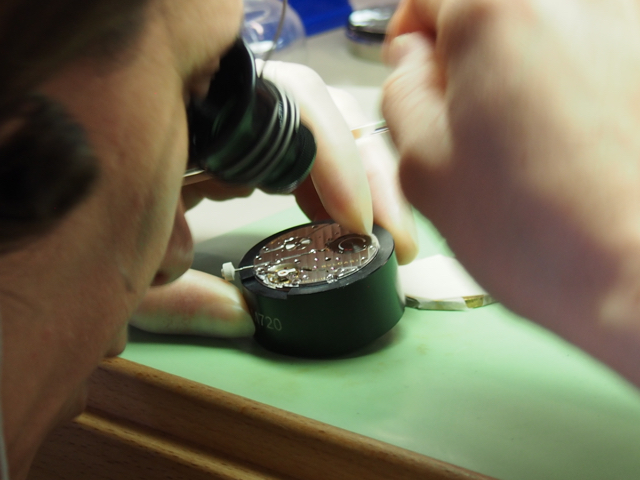
In the haute horology workshops of Bulgari, everything is done by hand. (Photo: R. Naas, ATimelyPerspective)
As if this wasn’t enough, secreted away on the top floor of the workshops is the cream of the crop: the chiming department. In this bright and airy space overlooking the Swiss countryside, four watch makers works side by side building, tweaking and finishing each and every chiming Bulgari watch.
The art and craftsmanship that goes into building luxury timepieces with the name Bulgari carefully placed on them is a feat that few could have expected just a couple of decades ago. Now, however, that same art, innovation and craftsmanship has become a benchmark standard for the brand.